In the early 1900s, German engineer Richard Mollier invented a graphic method of displaying the properties of various mixtures of air and water vapour. This device has different names in different countries - the i-x diagram, Mollier diagram, psychrometric chart - but the names all refer to the same object.
At first, the chart can be rather daunting because it displays so much information in a small space. However, once the basic information elements are understood, the chart becomes an essential reference tool when designing temperature and humidity control systems. It is the engineer's road map. It illustrates the starting place, the final position and, most importantly, how to get there.
Psychrometric terms and equations are described in detail in the ASHRAE Handbook of Fundamentals.
We have previously discussed the preservation type applications - the protection of artefacts, finished goods, buildings and raw materials from the effects of moisture. Process applications are entirely different. Generally speaking these applications provide an opportunity to enhance a manufacturing process by providing an optimum environment at all times regardless of the prevailing ambient.
Fundamentally, dehumidification is applied to prevent moisture regain or as an aid to product drying. If correctly applied, tremendous financial benefits are available to enhance and improve production techniques.
Moisture regain
Virtually every substance has some affinity for moisture. Even plastic resins like nylon can collect 6-10% of their dry weight in water vapour. In many cases this presents no problem. In others moisture regain can affect critical dimensions just like thermal expansion, or make products that would normally flow freely stick together.
Hygroscopic products are sensitive to high relative humidities rather than absolute humidities and the relative humidity can be high at any time of the year. In fact it is often higher in the winter than summer. When products are stored or manufactured at cool temperatures problems can be especially acute.
Typical industrial process examples preventing moisture regain are:
Confectionery packaging. Hard sweets often contain corn sugars and sorbital, both are highly hygroscopic. When the rh is high the product can absorb moisture and become sticky and often causing complete stoppages. Standard design condition for this application is 35% rh at comfort temperature.
Semiconductor and pharmaceutical clean rooms. In the manufacture of microcircuits hygroscopic polymers called photo resists are used to mask circuit lines for etching processes. If they absorb moisture, microscopic circuit lines are cut or bridged resulting in circuit failure.
In pharmaceutical manufacturing many powders are hygroscopic. When moist, they are difficult to process and have limited shelf life. Typical design condition for clean room applications is 25% r/h at 20ºC.
Safety glass laminating. The thin transparent plastic film which serves as the adhesive between layers of safety glass is quite hygroscopic. If allowed to absorb moisture, the film will boil it off in processing creating steam bubbles which get trapped in the laminated glass. The standard design for this application is 25% r/h at comfort temperature.
Pneumatic conveying. Operators of silos and conveying systems are well aware of the effects of high humidity levels. Blocked pipes, product quality and intensive maintenance are some of the obvious consequences. Compressing air increases the likelihood of condensation. When hygroscopic ingredients absorb moisture, they become sticky and build up inside the conveying lines with predictable results.
Desiccant dehumidifiers are extensively used throughout Industry to pre-dry the air before it enters the conveying system solving all the inherent problems associated with pneumatic conveying. The standard design for this application is 50% r/h or less at any temperature.
Product drying
Without question, product drying is one of the classic 'black arts' of industrial processes. Experience has shown very few companies understand the science that dries their products. They rely entirely on specialists who manufacture drying equipment often investing in capital equipment without any understanding of why they are doing so. In most cases products are dried in one particular way because historically they always have. Unfortunately, the lack of understanding of the principles of product drying cost Industry millions of pounds every year.
Most products are dried using hot air to vaporise moisture and carry it away. Often the hot air is either too slow or results in damage to the product. Enzymes, for instance, are destroyed by heat, and if yeast is dried with very hot air it cannot work properly.
It is essential for the engineer to understand that moisture migration is similar to heat transfer: there must be a temperature differential for heat to transfer, similarly, there must be vapour pressure differentials for moisture to transfer. The creation of vapour pressure differentials is what the equipment does, how great the differentials should be are determined by the process or product.
Every product has a drying characteristic at a given condition. Temperature, airflow across the product, moisture release rate, vapour pressure differentials, etc, are all key factors effecting the success of any drying regime.
Product drying applications for desiccant dehumidifiers has expanded significantly in recent years as clients examine the positive effects of low temperature drying on product quality and operating costs.
Typical process examples using dehumidifiers for product drying are:
Investment castings. In this process, wax patterns are repeatedly dipped in ceramic slurry. These layers build up to form a mould, which is filled with molten metal after the wax is melted out. Dry air (low vapour pressure) rather than heat is used to dry the ceramic layers because hot air could deform the wax pattern. Using desiccant dehumidifiers allows investment casters to operate foundries at a constant rate all year long, without having to allow for slower processing in humid months. This also allows solvents to be replaced by water. The productivity improvements are major - in many situations drying time is reduced by more than 50%.
Plastic resin drying.
All plastic resins are hygroscopic to some degree. The moisture they absorb boils off when they are heated by the moulding and extrusion processes when the plastic pellets are formed into products. This boiling vapour creates structural and cosmetic flaws in the finished product. Desiccant dehumidifiers are used to dry the plastic pellets to very low moisture levels before they are melted which improves the end product quality reducing waste and increasing productivity.
Confectionery pan coating.
The panning process for the confectionery Industry is very important to the finished product. It is also a difficult process. The product is placed in rotating drums and coating materials are sprayed into the drum over a period of hours to build up to the final coat thickness. The longer the process lasts, the more chance there is for the product to be damaged. Most panning processes involve chocolate-based products or products with temperature sensitive ingredients and the air used to dry the coating between sprays has to be kept cool. As heat cannot be applied to the product vapour pressure differentials can be increased significantly if the air supply is pre dried using desiccant dehumidifiers. This allows manufacture to operate at constant production rates throughout the year by eliminating ambient variations which traditionally have always affected the panning process.
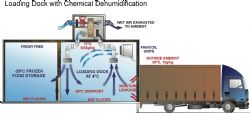
i
Design considerations
Industrial process applications mostly involve packaged systems with temperature and humidity control. Refrigeration plant looks after the heat loads and the desiccant drier takes care of the moisture loads. This combination is highly successful as each technology is doing exactly what it was designed for.
The central issue for design is to determine the optimum mixture of cooling and desiccant dehumidification techniques that will result in the lowest possible first cost and operating costs for a given set of circumstances.
Load calculations require a series of assumptions. In process applications they are beyond simple, quantifiable equations. Two well-qualified and experienced individuals working separately may well come to different conclusions on the same project. For best results, the system designer, equipment supplier, installing contractor and the end user should agree on the final value of each load element.
A system designer generally selects equipment based on peak-load requirements. However, to satisfy all the project requirements it is wise to understand how performance changes when operating conditions are different than extreme peak design.
Process desiccant dehumidification systems vary wildly in size, cost and complexity but they generally fall into three basic types according to their application: commercial hvac, industrial hvac and product drying.
In all of these systems the design process is essentially the same:
1. Define the purpose of the project
2. Establish control levels and tolerances
3. Calculate heat and moisture loads
4. Select, size and position components
5. Select and locate system control
Control levels and tolerances
Having defined the purpose of the project the control level and tolerances must be established. Research should be carried out if uncertainties exist. The greater the difference between the controlled space and the surrounding environment, the greater the load will be from each element.
The design condition is determined by the product or process. The important thing about the control level is that it must be specified in absolute terms (g/kg) before the calculation can proceed. For instance '30% rh' is not a useful specification because the moisture content of air at 30% r/h varies with temperature.
The temperature range for the control band must also be specified. The 'outside' conditions may include the internal surrounding condition as well as the external ambient weather but must be defined for moisture load calculations. Some judgement must be applied to the selection of these conditions. For standard design, weather data is available. When considering tolerances, instrumentation is a key factor. There is no point is specifying +/- 3% r/h if the instrument when calibrated only guarantees +/- 5%. Close humidity control is extremely difficult and expensive to achieve and most products do not require less than 5% control. Good quality humidity sensors are readily available and are far less expensive than costly dewpoint sensors.
Temperature control is far simpler as final trim is only dealing with sensible heat tolerances of 1ºC or less are achievable.
Calculate heat and moisture loads
This is best left to experts - usually reputable manufactures have application engineers who will assist and guide project engineers - alternatively they can be carried out by consultants.
Principal sources of loads are:
Moisture
Permeation through building: g/kg/m2
Evaporation from people: typically 100g/person/hr
Moisture release from products:
kg/h (wet weight - dry weight)
Wet surfaces: kg/h (v/press differential x surface area)
Combustion processes:
kg/h (firing rate x moisture release rate)
Air infiltration: min of 0.5 air change/h (vol x Dx)
Forced ventilation: kg/h if not pre-conditioned (vol x Dx)
Heat
Solar gains: kW (W/m2)
Personnel: typically 150W/person/hr
Machinery: kW
Product release: kW
Processing: kW
Infiltration: kW (minimum 0.5 air change)
Forced ventilation: kW
Select, size, and position components
Once the total moisture and heat loads are defined and agreed the system can then be configured. Temperature and humidity control systems will often involve heating, cooling, humidification and dehumidification. The question for the design then becomes how the components should be arranged.
Some typical arrangements are shown in Fig 1.
System 1. Pre-cool the make up air and dehumidify it with a desiccant unit before the air mixes with the return air from the room. When large volumes of make-up air are required this schematic is generally the most economic to install and operate.
System 2. Pre - cool the make-up air, then blend it with the return air before dehumidifying it with a desiccant unit.
System 3. Pre cool the mixed make-up air and the return air before dehumidifying with the desiccant unit. Cool air improves the performance of the dehumidifier increasing the capacity of the system and can allow the designer to use a smaller unit.
System 4. Mix the make up air and the return air before dehumidifying it with the desiccant unit - no pre-cooling. If the make up air does not carry a significant proportion of the moisture load it may be useful to pre cool in front of the desiccant unit.
Select and locate system controls
Fig1: Typical dehumidification processes
Instruments can measure the rh of air, its specific humidity, and the moisture content of solids. They also measure the temperature. The operation of each instrument is different. The key function of the project will determine the control philosophy. Once established suitable instrumentation can be selected.
There are four basic functions the instruments can perform: humidity and temperature sensing, display, recording and control. Each function and final result is limited by the instruments repeatability (precision), range, response time and durability. Each must be considered by the design engineer and the location within the system suited to each instrument. The sensor placement is often more important than the sensor accuracy.
Performance of desiccant dehumidifiers
Desiccant dehumidifiers all function in the same way - they remove water from the air using the vapour pressure differences between the air and the desiccant surface to attract and release moisture.
The performance of the desiccant drier is affected by the moisture content, temperature and velocity of the process air through the desiccant. It is also affected by the moisture content, temperature and velocity characteristics of the reactivation air. The performance is also affected, of course, by the mass of desiccant presented to the process and reactivation air streams and the desiccant sorption and desorption characteristics.
In general, at a constant temperature, each desiccant has a fixed capacity to absorb moisture. Its capacity is a function of relative humidity. Change either one and the capacity is affected.
The dehumidifier performance assumes one basic assumption - the unit is operating at equilibrium. In other words, the total energy on the process side is balanced by the energy in reactivation. If the system is not in equilibrium (airflow's not balanced, filters blocked, etc) the dehumidifier will not perform in a predictable manner.
Typically, the standard depression across a desiccant rotor is 5 to 6g/kg
Low dewpoint systems
It is not possible to achieve low dewpoint using cooling equipment. It is possible using desiccant dehumidifiers.
A typical application would be a blast freezer operating at a temperature of -35ºC.
When ambient air infiltrates into the freezer, moisture carried by the air ends up as ice on the evaporators which eventually stops production. By creating a positive pressure within the freezer ambient air does not infiltrate and the freezer can operate for much longer periods before defrosting.
To create a positive pressure requires a supply of dry air at or below the dewpoint condition the freezer operates at. In this case the air would be dried to a condition of around 0.079g/kg equivalent to -40ºC dewpoint. A standard dehumidifier could not reduce ambient air from 13g/kg (summer maximum for design) to this low condition.
The system would be configured with pre-cooling using either DX refrigeration or chilled water to give a supply condition to the desiccant at 5ºC and 100% rh (5.4g/kg). The dehumidifier would then further dry the air to the required dewpoint. Sensible heat gains are not normally a concern for this application as the reduced latent load on the freezer far exceeds this value.
A desiccant drier can be installed inside a room as an individual item or form part of a complex system. Large rotors can handle up to 80,000m3/h airflow assembled as an air handling unit with all ancillary equipment pre fitted.
Maintenance of desiccant dehumidifiers
Fundamentally, there are only three moving parts to a desiccant dehumidifier: rotor, process air fan, and reactivation air fan. Typically in Industrial applications the life of a desiccant rotor would be up to ten years. Some rotors still exist after 25 years in field operation. Planned maintenance is an essential part of a desiccant system and should not be neglected.
With thanks to Mike Creamer of Business Edge who revisits his Masterclass series of articles, updating and adding to the information which proved so useful to readers when the series was first published over ten years ago. In this reincarnation, the series will cover both air conditioning and refrigeration and serve as an on-going source of technical reference for experienced personnel as well as providing a solid educational grounding for newcomers to our industry.