Scroll Compressors
The scroll is a simple compression concept centred around the unique involute spiral shape of the scroll and its inherent properties. Two identical scrolls are mated together forming concentric spiral shapes. The concept was proposed almost 100 years ago but has only relatively recently been developed to practical engineering and mass production levels.
As shown in Fig 1, during compression, one scroll form (fixed scroll) remains stationary while the other scroll form (orbiting scroll) is allowed to orbit around it. Note that the orbiting scroll does not rotate or turn but merely orbits the stationary scroll. The orbiting scroll draws gas into the outer crescent-shaped gas pocket created by the two scrolls. The centrifugal action of the orbiting scroll seals off the flanks of the scrolls.
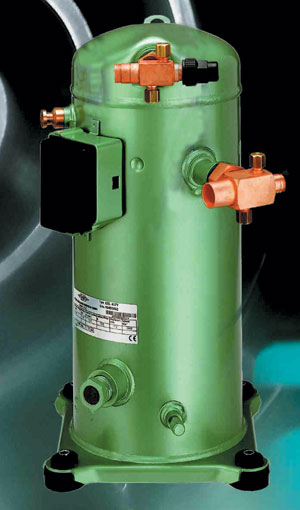
As the orbiting motion continues, the gas is forced toward the centre of the scroll and the gas pockets become compressed. When the compressed gas reaches the centre, it is discharged vertically into a chamber and discharge port in the top of the compressor. The discharge pressure, forcing down on the top scroll, helps seal off the upper and lower edge tips of the scrolls.
During a single orbit, several pockets of gas are compressed simultaneously, providing smooth, continuous compression. Both the suction process (outer portion of the scroll members) and the discharge process (inner portion) are continuous. When compared to piston compressor technology, the scroll compressor offers several significant advantages:
Figure 2: In a scroll compressor, only two components, a fixed scroll and orbiting scroll, are required to compress gas
Simplicity – Only two components, a fixed scroll and orbiting scroll, are required to compress gas. These two components replace the approximately fifteen components in a piston compressor, which are required to do the same work.
Figure 1: Operation of the scroll compressor
Efficiency - The Scroll compressor offers three efficiency advantages over a piston compressor:
1 The suction and discharge processes of a scroll compressor are physically separated, reducing heat transfer between suction and discharge gas. In a piston compressor, the cylinder is exposed to both suction and discharge gas, resulting in high heat transfer. This reduces the efficiency of the compressor (see fig 3).
2 The scroll compression and discharge process is very smooth. A scroll compresses gas in approximately 11/2 revolutions as compared to less than half of a revolution for a piston compressor. The discharge process occurs for a full 360° of rotation versus 30-60° of rotation for a piston compressor.
3 The scroll compressor has no valves. While a piston compressor requires suction and discharge valves, the scroll design does not require a dynamic valve. This eliminates all valve losses. The result is that the scroll compressor is inherently 10-15% more efficient than a piston compressor.
High Volumetric Efficiency
A scroll compressor has no clearance volume. All gas that is trapped in the compression process in the outer pocket of the scroll members is released through the discharge port. This means that the scroll compressor inherently has a higher capacity than a piston compressor at extreme operating conditions.
Noise Level
A scroll compressor has extremely limited motion, which, unlike a piston compressor, can be perfectly balanced. Because suction and discharge flow is continuous, a scroll compressor has very low gas pulses. No dynamic valves equals no valve noise, a common problem in a piston compressor, is not a factor.
Durability
While a piston compressor has been designed to be durable in all types of systems, significant design effort and system cost is required to protect the compressor from liquid slugging and debris in the system. A scroll compressor can be designed to be compliant to both liquid and debris. This can be done by allowing the scroll forms to separate from each other in the presence of contaminants or liquid. This feature allows a compliant scroll compressor to have superior tolerance to liquid and debris. Compliance has the added benefit of allowing the scrolls to “wear-in” over time; that is, to increase compressor and system efficiency with running time. Compliance refers to the method in which the two scroll members interact to achieve high efficiency and durability simultaneously. The unique and patented Copeland Compliant Scroll Compressor, with both radial and axial compliance, has several advantages:
Figure 3: In a scroll compressor, the suction and discharge process are physically separated, reducing heat transfer between suction and discharge gas.
Figure 4: the scroll compression and discharge process is very smooth. A scroll compresses gas in approximately 1 1/2 revolutions as compared to less than half of a revolution for a piston compressor. The discharge process occurs for a full 360degrees of rotation versus 30-60degrees for a piston compressor.
Figure 5: The scroll compressor has no valves. While a piston compressor requires suction and discharge vlves, the scroll design does not require a dynamic valve.
1 Continuous flank contact, maintained by centrifugal force, minimises gas leakage and maximises efficiency.
2 Radial compliance allows the scroll members to separate in the presence of liquid refrigerant or debris, eliminating high stress in the members and substantially improving the durability of the compressor.
3 Axial compliance allows the scroll tips to remain in continuous contact in all normal operating conditions, ensuring minimal leakage without the use of tip seals. This means the scroll performance will not degrade over time because there are no seals to wear and cause gas leakage. Because of the radial and axial compliance feature, the Copeland Compliant Scroll Compressor has unprecedented liquid handling capability. In addition, it is designed to start under any system load. Combined, these characteristics simplify the system design, reduce the system operating costs and increase the durability of the system.
NEXT MONTH: Rotary vane, screw and centrifugal compressors
With thanks to Mike Creamer of Business Edge who revisits his Masterclass series of articles, updating and adding to the information which proved so useful to readers when the series was first published over ten years ago. In this reincarnation, the series will cover both air conditioning and refrigeration and serve as an on-going source of technical reference for experienced personnel as well as providing a solid educational grounding for newcomers to our industry.