Gourmet food specialist FrischeParadies uses state-of-the-art equipment to cool its food. The company is using an R134a/CO2 cascade system with compressors and Varipack frequency inverters from Bitzer at its new supermarket in Stuttgart.
The supermarket has been designed architecturally in the style of a modern market hall: its atmosphere makes it ideal for selling high quality food and its equipment is state of the art.
The retailer said: “Every year, we have to refrigerate more than 21,000 tonnes of food and display more than 12,000 high-quality delicacies in our supermarkets, including selected fish and extraordinary meat products. Top quality and freshness are our highest priorities.
“The cooling chain always has to work – optimally, not just barely. For this reason, following in-depth consultation with Michael Müller from the engineering firm Eneratio in Hamburg, we have selected an R134a/CO2 cascade system.”
“The solution is technically ideal and gives us numerous advantages in terms of energy efficiency, cost-effectiveness and operating reliability. That is why we carefully selected our partners. Freshness is our trade. Naturally, this also goes for our new Stuttgart branch with its 68 members of staff.’
The R134a/CO2 cascade system manufactured by compact Kältetechnik GmbH and installed by Kratschmayer GmbH, which specialises in consulting, construction, service and maintenance of refrigeration and air conditioning systems, will reliably keep the gourmet products at an ideal temperature. Both companies have more than 20 years of experience in refrigeration and air conditioning technology.
Uwe Schmid-Böcker from Kratschmayer said: “Reciprocating compressors and Varipack frequency inverters from a single source: Bitzer. This is a crucial advantage for a system where reliability comes first. ‘We can be sure that the quality is high and that both components are optimally compatible with one another.”
The Varipack frequency inverters were connected to the control units planned and built by Kratschmayer in close coordination with Bitzer and the regulatory component supplier Wurm.
Bitzer was on-site for the initiation of the system in order to advise and assist the customer with its first refrigeration system featuring Varipack frequency inverters.
Benjamin Vornweg, a technical consultant at Bitzer, said: “Naturally we do not leave customers in the dark with our compressors and frequency inverters, even if there are specialists as experienced as Kratschmayer on hand. For instance, we assisted in the configuration of the Varipack frequency inverters in FrischeParadies so that we would be able to look over the customer’s shoulder and see how easy it was to configure and commission our product solution. Ultimately it gives the customer extra peace of mind to know that the system has been connected properly and the goods are absolutely safe.”
Bitzer also provides another type of security for system operators: the Varipack frequency inverters have been specially designed to be easy to install and operate. Additionally, the Varipack frequency inverters and Bitzer reciprocating compressors have been adapted in order to optimise their compatibility with one another.
Both system components in FrischeParadies, the R134a and the CO2 stage, feature a smart Varipack frequency inverter from Bitzer. These frequency inverters ensure that the capacity control is highly precise and safe. The frequency range of the Varipack in FrischeParadies is 25 to 70Hz for the six-cylinder compressor for medium-temperature applications (R134a stage) and 30 to 65Hz for the two-cylinder compressor for low-temperature applications (CO2 stage). The speed of 65Hz meets the requirements of the customer. Generally speaking, CO2 compressors from Bitzer can be run at up to 70Hz for subcritical applications.
A total of five Bitzer Ecoline reciprocating compressors work in the R134a stage (one 6GE-30Y and four 4FE-25Y models). The 6GE-30Y is operated by an FHU+73 Varipack frequency inverter. This allows the compressor’s output to be adjusted to meet the actual demand, which results in excellent system efficiency and control quality. The R134a manages the temperatures of the medium-temperature consumers and dissipates the waste heat of the CO2 stage.
Four Bitzer Octagon reciprocating compressors (2ESL-4K) are used in the CO2 stage. In this stage too, one of the compressors is operated by an FEU+16 Varipack frequency inverter. The purpose of the CO2 stage is to manage the temperatures of the low-temperature consumers.
Benjamin Vornweg said: “The intelligent Varipack frequency inverters have been specially adapted to the refrigeration technology and the operation of Bitzer refrigeration compressors, and are compatible with all Bitzer reciprocating compressors. The Varipack product range is also easy and intuitive to commission.
“It therefore provides users with exceptionally user-friendly and safe capacity control. Another advantage of the Varipack frequency inverter is its modular design. This allows for a wide range of applications, for example in supermarkets, hotels, restaurants and food production.’
The Varipack product range is compatible with refrigeration and air conditioning systems as well as heat pumps. It can be integrated into individual compressors and compound systems alike.
The optimised adaptation of Varipack frequency inverters to Bitzer reciprocating compressors makes it possible to accurately set refrigeration systems to meet current cooling demand, which reduces energy consumption and cuts running costs. Another advantage of the Varipack frequency inverter is that it can be operated in two ways. They are either dependent on an external set point signal – as in the case of FrischeParadies – or they can regulate smaller systems with up to two compressors with an optionally available extension module. In this case, the Varipack frequency inverters regulate the evaporation and condensing temperatures and can switch on a second fixed-frequency compressor. They can also be fully integrated into the switchboard or mounted via push-through installation. In the push-through installation variant, the rear part of the frequency inverter that is to be cooled is ‘pushed’ through the switchboard wall in order that the waste heat does not affect the interior of the switchboard.
The Varipack is extremely easy to commission thanks to its preconfigured BEST (Bitzer Electronic Service Tool) software.
Besides managing the frequency inverters, the master control system from Wurm carries out all regulatory, control and monitoring tasks. Of particular note is the special heat recovery module which was designed to manage a heat recovery circuit by feeding waste heat from the R134a stage into a 15,000 litre water tank.
A specially programmed main module from Wurm also manages peripheral system components such as pumps, ventilators and a glycol circuit. All control circuits can be operated and integrated into remote data monitoring with the Frigodata software.
Compressors are the heart of every refrigeration system and a heart should be as strong and powerful as possible. Kratschmayer and compact count on Bitzer products to meet the high requirements of FrischeParadies. Five Ecoline reciprocating compressors from Bitzer work in the air-cooled R134a stage and ensure that the display cabinets and cold stores are always at the right temperature. The main components of this medium-temperature application stage are a frequency-controlled six-cylinder Ecoline compressor with a displacement of 110.5m3/h (50Hz) and four four-cylinder Ecoline compressors, each with a displacement of 101.8 m3/h (50Hz). Thanks to their outstanding cooling capacity and low energy requirements, the compressors of the semi-hermetic Ecoline range are ideal for efficiently operating refrigeration systems under both full and part load.
In the CO2 stage for low-temperature applications, four two-cylinder Octagon compressors designed by Bitzer for subcritical applications keep display cabinets, cold stores and ice cream machines running. Each of them has a displacement of 7.8m3/h (50Hz). 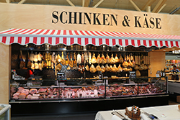