WHEN something goes wrong with the building services the usual course of action is to call in a service/contracting company with the necessary resources to fix the problem. If the equipment manufacturer or installer provides such a service under a warranty or service agreement, then this may be a satisfactory solution. The question that has to be raised in this scenario is how cost effective is it to have separate service agreements for each component within the building? Also, in older buildings tracing the OEM or installer can be a problem. The route that a number of companies are now taking is to appoint a specialist maintenance company.
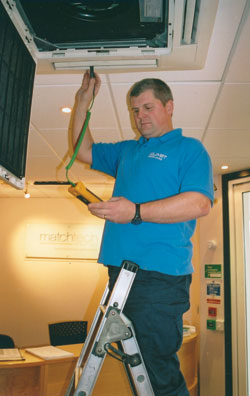
Matchtech Group Plc is one company that has adopted this strategy, appointing Clivet Aircon to take on the maintenance of a range of services at its Fareham HQ. Matchtech is one of the UK’s largest recruitment consultancies covering engineering, construction, scientific and IT sectors. With some 200 employees on site, keeping the premises fully functional and in pristine condition while ensuring the comfort of its employees is a priority. The seven-year old building that Matchtech moved into five years ago was built without air conditioning. A system using ceiling-mounted split chillers was installed at a later date to complement the original central heating infrastructure.
“We brought in Clivet Aircon in 2005,” says Pam Beecroft, administration manager at Matchtech. “We had already recognised that having one supplier with suitably qualified engineers made logistical and economic sense.”
Clivet Aircon undertook a thorough review of Matchtech’s requirements and produced a service schedule that included a set of protocols and checks to ensure that all work is fully implemented and regularly recorded. Engineers visit at set intervals and times that fit in with Matchtech’s operations and, should a problem arise, then an engineer with the necessary security approval and knowledge of the site is always available.
Where servicing and maintenance is being outsourced, then the provider must be able to advise the client as to their health and safety responsibilities and if requested, ensure that all equipment is fully compliant.
Clearly, all new equipment will be compliant, but this should not be seen as an excuse for putting off maintenance, says Clivet Aircon. The company recommends that a programme of condition monitoring should be established by the provider at the outset, as this will enable the client to obtain the best possible life from the equipment, the company maintains. If, however, there is a form of equipment write-off or renewal policy at the end of a set period, the maintenance provider should establish effective dates for equipment replacement and how it is managed cost-effectively.
When selecting a company, Clivet Aircon suggests that the building manager ensures potential providers have the necessary qualifications and trained staff to deal with fault finding, fault prediction and component servicing and replacement. Undertaking a comprehensive audit that compares the capabilities internal to the company with those offered by an outsourcing supplier should be a fundamental component in the decision-making process. Factors that should feature in this audit include cost, quality, delivery, control and exploitation.
Selecting the right provider is essential to the success of the outsourcing decision, as the supplier effectively becomes the offsite maintenance department.
Clivet Aircon
02392 381235