Walk-in cold rooms are essential structures in the food retail and Ho.Re.Ca. (hotels, restaurants and cafes) businesses. Being on 24 hours a day, seven days a week, they represent a significant share of the energy bill in these enterprises as well. Around the globe, energy savings have been on the agenda for some years now, but at this moment in Europe, with the crisis in the region, caused by the Russia versus Ukraine conflict, energy prices are pushing the demand for energy saving technologies more than ever.
In scenarios like this, technology migrations get accelerated. The migration for R290 refrigerant in commercial refrigeration started years ago, mainly pushed by regulations but also by big end users (like supermarket and restaurant chains) that have been establishing carbon footprint reduction goals. That is because R290 has a global warming potential of 3 (with new studies concluding that it is below 1), and has been the alternative chosen to replace HFC refrigerants in many kinds of self contained refrigeration applications. 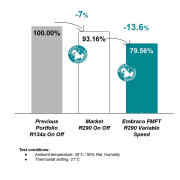
In the last year, the migration to R290 has gained more speed also in niche applications such as cold rooms, already helping to save energy. R290 is by nature a very energy efficient refrigerant, when compared to other options: it has a low final compression temperature, which means that the compressor works at a low temperature regime, and this also contributes to the energy efficiency and the reliability of the compressor.
Nonetheless, there is much more that can be done in terms of saving energy, if we combine technologies, more specifically: to bring together the thermodynamic properties of R290 refrigerant with the capabilities of variable speed compressors into packaged refrigeration units for walk-in cold rooms, systems also known as monoblocks (compact units in which the condenser and the evaporator are placed in a single tower that is installed through a wall or ceiling within the cold room).
Variable speed technology is still new for cold rooms. But we see it as a trend in formation, due to the fact that it is a technology that can take the monoblocks, already a traditional solution for cold rooms, to a new level of performance.
Almost 14% energy savings
In our most recent case study, a monoblock for walk-in cold rooms with R290 and variable speed technology reached 13.6% of energy savings in comparison with a fixed speed similar (on-off) solution also running on R290, in medium temperature conditions (EN17432). This energy saving also represents a similar percentage reduction in the total equivalent warming impact (TEWI) and 13% reduction in the cost of ownership.
The study was made with Daikin’s new LMSEY series, a lineup of wall-mounting R290 monoblocks for walk-in cold-rooms equipped with Embraco FMFT variable speed compressors. The LMSEY series monoblocks are plug and play, self-contained, hermetically sealed systems with R290 refrigerant charge below 150 g. It also uses microchannel condenser, expansion valves, and electronically commutated (ECM) fans, to improve energy efficiency.
How does variable speed work?
Variable speed technology saves energy because it counts on an electronic device, named inverter, to control the compressor’s motor. Inverter and motor compose a system that can modulate the cooling capacity by adjusting the compressor’s working speed: reducing it during low demands (low ambient temperature or no door opening) and increasing it under high demands (pull down, reload or high ambient temperature). This enables the compressor to use only the amount of energy required at each moment and nothing more. 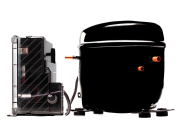
When you have a fixed speed (on-off) compressor, it operates at a constant speed, continuously switching on and off to meet the refrigeration equipment’s cooling demand. This pattern requires abrupt power loads when starting and, for having only one speed, it always works at full capacity until it turns off, when the target temperature is achieved. It leads to wasted energy.
Putting it in numbers: a variable speed compressor can work in a range from 1,600 up to 5,000 rpm (rotations per minute), whereas a fixed speed only runs at the power supply frequency (3,000rpm for 50Hz and 3,600 rpm for 60Hz).
The capacity modulation also delivers lower noise and vibration and allows to keep food fresh for longer, by maintaining better temperature stability inside the cold rooms. It happens because this technology overcomes temperature variations much faster than the standard on-off compressors models, thus improving food preservation and potentially avoiding product loss.
The variable speed compressor also enables yet an additional saving, in stock management. Because the inverter has a wide voltage input, it allows the final product, in this case, the monoblock, to cover all the needs of a global market just with one single model.
Quick gain for refurbishments
Combining the migration to R290 and variable speed in one single move can be the answer to saving the maximum energy possible and, in the case of cold rooms, the use of a monoblock to do it is versatile, independent of the size of the cold room. This particular series used in the case study can refrigerate a room up to 24 cubic meters, and the units can be combined to up to five. 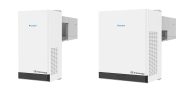
We can’t also forget that cold rooms are impacted by other issues, not only energy consumption, such as: space restrictions, in the case of small and medium enterprises, and the necessity for a system that is of easy maintenance, fast installation and smooth operation. Monoblocks are compact systems and don’t depend on extensive external fittings, thus being fast and simple to install and of low maintenance. In the case of refurbishment of existing cold rooms, combining all these technologies is a way to reduce energy costs and environmental impact in a quick and simple manner.