The recent sharp rise in energy costs is focussing minds on ways to improve efficiency and reduce the cost of operating refrigeration plant. Government support for household energy bills has taken at least some of the sting out of price increases for homeowners. However, industrial and commercial users who's businesses depend on cooling are being hit hard.
For some, particularly in food manufacture and processing, cooling energy costs may account for more than 70per cent of their energy bill. It’s no wonder that controlling and reducing energy used in refrigeration is now a board-level issue.
A key principle in any energy efficiency drive is ensuring refrigeration equipment delivers the right amount of cooling to achieve its purpose. Over-refrigerating, or poor system optimisation, is money down the drain – and entirely avoidable.
Variations in load and changing ambient conditions in our climate mean that most refrigeration systems are not required to operate at full capacity for long periods. In the vast majority of cases (data centres being a notable exception), part-load operation is likely to be the default condition.
It is therefore vital to ensure systems are optimised at part load to ensure efficient operation and that running costs are kept as low as possible over the lifetime of equipment.
One way of doing this is by the use of current inverters. These sophisticated devices modify the electrical power input to the compressor motor in response to changes in load, slowing down or speeding up the compressor to match cooling output with demand. Implemented correctly, and properly matched to the system, inverters are very effective and significantly improve refrigeration efficiency and performance.
The downside, of course, is that inverters can be expensive and add a significant additional upfront cost when purchasing new equipment. If poorly implemented, they can also cause interference problems with nearby electrical equipment.
Bitzer has developed a lower-cost alternative to cooling capacity control that does not depend on inverters, which is highly effective and without the high capital cost and potential interference issues.
The CRII–Varistep control system enables proportional modulation of compressor output in response to changes in load and system conditions, giving stepless capacity adjustment from 50% up to 100% as standard, and 10% to 100% as an option.
It uses a different approach to managing capacity control, based on the principle of incrementally blocked suction. This uses hollow control pistons in combination with a bespoke algorithm to enable fine, fast-reacting control of compressor output.
The control algorithm – the system's brain – constantly monitors and adjusts output via mechanical actuators. The algorithm in each case is configured according to operating conditions and refrigerant, allowing very precise control and excellent system optimisation.
The system is used on Bitzer's Ecolite 2.0 condensing units, now available for use with A2L refrigerants, including ultra-low GWP R1234ze/yf, and lower GWP R455A and R454C.
Designed for use in a wide range of applications, such as cold rooms, petrol stations and convenience stores, Ecolite condensing units are available from 1.5 kW to 5 kW in low temperature versions and from 3.5 kW to 16 kW in medium temperature versions. Operating range spans -45°C up to 0°C, without requiring liquid injection.
Despite its competitive price point, Ecolite delivers excellent energy efficiency through a combination of this inverter-free capacity control, plus optimised heat exchangers and variable-speed fans.
The ability to vary fan speed according to changes in load and ambient conditions delivers further significant energy savings. Ecolite uses the latest technology in this field, with integrated EC motors and fans encapsulated in an aerodynamically-optimised housing.
The speed of the fan is constantly adjusted, so it maintains desired head pressure for the required duty. This happens automatically, come rain or shine, and is managed by the integrated onboard controller.
As well as providing constant load-matching and saving energy, variable-speed fans can reduce maintenance and extend the operational life of equipment, again saving cost.
Another benefit is that variable speed fans reduce noise levels at part-load, increasingly important in applications near residential areas or sensitive locations, such as hospitals.
Heat exchange is another key area of plant operation that is vital to optimise for maximum efficiency. To ensure this, heat exchangers on Bitzer condensing packages are precisely matched to each unit, taking into account size, capacity, performance envelop and refrigerant.
Recovering heat from refrigeration systems that would otherwise be wasted also presents further opportunities to enhance efficiency.
Following successful field tests, Bitzer recently added a new heat recovery option to Ecolite, which further boosts efficiency. The design (pictured) enables end users to harness heat from the condenser that would otherwise be wasted to air, to produce hot water. 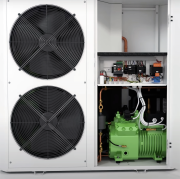
Heat recovery connections are installed on the condenser during manufacturing at the factory, and operate in combination with an oil separator and check valve.
The outlets enable the unit to be connected to an external plate heat exchanger and/or water tank, to extract and store the recovered energy in the form of hot water. This can then be used for process applications, heating or domestic hot water.
High energy prices are clearly unwelcome, adding pressure to businesses and further fuelling the monster of inflation. However, if there is an upside it is that they force us to consider again what we can do to improve energy efficiency, which is in the interests of all, not least the planet.
It is also a sobering reminder, if one were needed, that when it comes to investing in equipment, 'cheap isn't always cheerful'. A well designed and built system costing, say, 10 per cent more than a bargain-basement alternative, can save this small premium many times over during its lifetime through better efficiency and more reliable operation.
It has always been true that by far the greatest cost of owning refrigeration plant is the energy consumed during its lifetime. The recent price rises have tilted the equation even further in this direction.
Investing a little more in better equipment at the outset makes even more sense today.