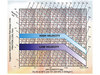
Table 1: Suggested velocity and friction rate design limits
Additional information that has to be determined is the pressure drop required by the discharge diffusers in order to achieve the required distribution characteristics.
This figure will have to be added to the duct pressure loss together with losses from all components, such as inlet louvres, filters, pre-heaters, etc, fitted before the fan and between the fan discharge and diffusers.
Velocity reduction
This method of calculation is based on setting the initial velocity at the beginning of the main duct, in accordance with the recommended velocity for the given application as shown in Table 2.
Table 2: Recommended duct velocities
This velocity is then reduced by an arbitrary amount after each junction. The reduction of velocity at each junction will be influenced by the number of junctions from the main duct. The object is to maintain a velocity greater than the recommenced velocity for a branch duct at the last duct junction.
Having determined the velocity, it is then a simple matter to calculate the required cross sectional area required to achieve this figure using the formula:
Where
V = velocity in m/s
Q = air volume in m3/s
A = cross sectional area of duct in m2
Therefore the area A = Q/V
Thus A = ?r2 and r = 1?2D so
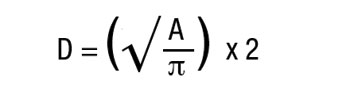
If rectangular ducts are to be used then enter the chart giving circular equivalents of rectangular ducts by converting D from m to D in mm. Then select the desired length of one side in mm and move horizontally until the dimension of the diameter is found. If necessary, interpolate between rows or columns.
Calculate the total pressure drop of the longest run, taking into consideration all fittings in the run, (generally the longest run has the greatest pressure drop but a shorter run with a large number of fittings may have a greater pressure drop, therefore unless it's obvious which run has the highest loss it will be prudent to undertake check calculations on other runs.) The highest pressure drop run is called the Index Run. This figure will be used to select the fan.
To minimise balancing of duct flows, a check calculation should be performed to establish the pressure loss in each of the branches, then duct dimensions adjusted to equalise the losses to ensure the correct pressure is available at each diffuser.
Return duct design should be undertaken in a similar manner with the highest velocity located nearest the exhaust fan or discharge outlet.
Equal friction
As the name implies this method of design is based on all duct runs having the same friction loss. The starting velocity is selected using Table 3 - Maximum Velocities. Using this figure in conjunction with the total volume of air to be supplied, enter Table 1. With the total volume of air expressed in litres per sec (l/s), move vertically along the volume line until it intersects with required angled velocity curve and at the intersection of these two lines, traverse horizontally to read the fraction loss in Pascals per metre (Pa/m). Note the name fraction, not friction. This is because we are looking at the pressure loss per unit length.
All remaining duct selections will be at the same pressure loss established above. All that has to be done is to enter all subsequent air volumes on the 'x' axis and read the velocity at the point of intersection with the pressure loss line. However care has to be taken to ensure that the velocities resulting from these readings do not exceed the maximum velocities recommended. If this does occur, then a lower starting velocity should be used. The total length of each run must be calculated including the equivalent length of all fittings and this figure is then multiplied by the fractional pressure loss to establish the total loss of the duct run. The fan is then selected to match to the total loss figure.
Table 3: Typical air velocities/maximum velocities
Static regain
A simplistic explanation of this method of calculation is to say that the object of this is to ensure that the same pressure is available at each take off point by converting velocity head pressure to static pressure, ie static regain. The conversion of velocity head takes place after each branch and is calculated to match the loss in the length of duct up to the next branch. With this method of calculation, the balancing of the system is made much easier and there can be cost savings resulting from the reduced need for balancing dampers.
In order to explain the static regain method of calculation fully, it is necessary to use an example and follow the calculation process, step by step. However in order to do this, a number of additional charts and tables will be required, but insufficient space is available to incorporate these charts in this month's article and these will be included next month.
Constant velocity
The constant velocity method of calculation is usually restricted to dust and fume extraction systems where the object is to entrain dust particles in the air stream. The velocity must be maintained at a sufficiently high level to carry the particles to a collector receptacle. The velocity is then reduced to a level which will no longer support or suspend the particles and they then simply drop out of the air stream for collection. See the Contaminant Transport Velocities and Contaminant Capture Velocities in Part 30 next month.
With the above parameters established we can prepare to design the duct system. However, correct duct design requires the following information at various points in the design process:
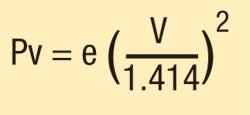
Where Pv is velocity pressure in Pascals
and e is air density in kg/m3 (standard air = 1.204kg/m3)
When working with standard air this formula can be reduced to:
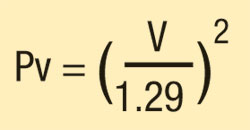
To assist Table 4 below shows velocity v velocity pressure.
In order to arrive at the most efficient ductwork design, an iterative process is required. When starting the design, a number of arbitrary parameters are used to establish dimensions and pressure losses throughout the system.
On completion of the duct layout, the calculated friction losses may show an excessive loss and the section of duct at the root of this can be identified. Therefore, an adjustment in sizes will be required which may result in the main duct and/or the branch duct dimensions and types of elbows and branches being altered.
For example, from a cost aspect, splitters and turning vanes may have been omitted. However, the resultant friction losses could have shown that these cost savings are offset by increased cost of a larger fan assembly.
After the duct design has been altered the losses will have to be recalculated.
There are a number of computer duct design programmes that can speed the process but not all programmes can optimise the design. Since it is the optimising process that is time consuming and determines the effectiveness of the installation, this feature should be sought after in any programme you may consider purchasing.
The design velocity can be determined from Table 2 which shows a number of different applications and the recommended velocities for each of them. The table differentiates between applications that have noise as the primary consideration and those that have duct resistance as the controlling factor.
figure 1
With thanks to Mike Creamer of Business Edge who revisits his Masterclass series of articles, updating and adding to the information which proved so useful to readers when the series was first published over ten years ago. In this reincarnation, the series will cover both air conditioning and refrigeration and serve as an on-going source of technical reference for experienced personnel as well as providing a solid educational grounding for newcomers to our industry.