16 October 2009
Skandia chooses Turbomiser chillers for UK headquarters re‐fit
Global financial group saves thousands of pounds a year, with double chiller replacement at UK headquarters. Andrew Bailey reports.
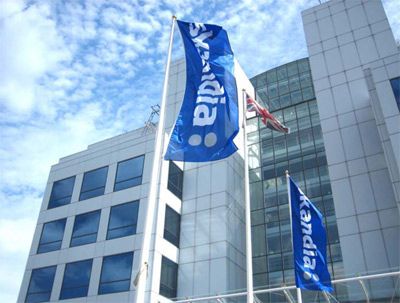
A major chiller replacement project at Skandia’s landmark building in
Southampton will save the global financial services company an
estimated £20,000 a year in energy costs.
The company has
replaced two existing chillers operating on R407C refrigerant with
ultra-efficient Turbomiser machines, manufactured by Italian company
Geoclima and supplied by UK distributor Cool-Therm (UK) Ltd.
The
units are delivering immediate energy savings and a high quality
working environment for the company’s 1000 plus headquarters staff. The
chiller replacement is part of a major upgrade by Skandia of its
facilities in Southampton. The three year project has involved
investment in new IT systems, building modernisation, and a drive to
cut carbon emissions and improve energy efficiency.
The project
involved replacing two original screw compressor-based chillers with
new 1.05MW Turbomiser units, based on oil-less magnetic bearing
centrifugal compressors. One of the existing units was a freecooling
chiller, requiring the building’s entire chilled water system to be
filled with 25 per cent glycol to minimise the risk of freezing. This
required in excess of 20,000ltrs of glycol
The previous
free-cooling approach also relied on significant inputs of pump and fan
power, and reduced the efficiency of heat exchange in air handling
units and fan coils around the building. Because of the exceptional
energy performance of Turbomiser technology at all seasonal conditions,
it was possible to overcome the need for an expensive glycol-based
system – while achieving improved performance and efficiency.
The
Turbomiser is a new type of “ultra efficient” chiller that delivers
exceptional energy savings and reduction in carbon emissions, while
ensuring high quality comfort for building occupants. It achieves this
by harnessing a combination of several innovative technologies, which
together deliver unprecedented energy savings.
These include:
- Inverter-controlled Turbocor compressors whose output can be precisely matched to load;
- Micro-channel aluminium condensers, that reduce refrigerant charge while increasing the effectiveness of heat exchange;
- Flooded evaporators that ensure optimum energy transfer between refrigerant and water;
-
Use of a liquid refrigerant pump system that significantly increases
thermodynamic efficiency across the chiller’s operating range;
- Speed control on fans to match performance to demand and reduce energy consumption;
-
A sophisticated chiller control system that integrates with that of the
onboard compressor control to optimise performance of the whole system.
As
a result, Turbomiser requires between a third and a half of the energy
used by conventional screw or reciprocating- based chillers.
The
chiller replacement was required following performance problems and
breakdowns in the previous installation. An investigation showed that
pipework modifications since the original system was installed had
resulted in the two chillers working against each other.
The
project required rectifying pipework layout to stop conflicts, and
removal and replacement of the chillers. An important design issue for
the chillers was to ensure that all pipework connections were
positioned and engineered to the millimetre, to match those of the
existing installation and enable rapid and effective replacement.
To
achieve this, one Turbomiser chiller was designed as a left-handed unit
and the other as a right-handed unit – to dovetail with the existing
building services design. Control panels for the chillers were designed
and engineered with equal precision, to ensure that when craned into
position they were accurately located inside roof-top plant rooms,
making service and maintenance activities easier and safer.
Given
the coastal location, the microchannel condenser coils in the roof-top
mounted units are epoxy coated to protect against the corrosive effects
of maritime air.
The chillers, painted in a bespoke colour (RAL
9018) to match the architecture of the building, are also equipped with
side screens to protect against incursion by nesting seagulls. The
change-over on the top of the nine-storey city centre building required
meticulous planning. The lifts took place in full view of the public
and adjacent local government offices.
Ralph Birch of Prima4,
who project managed the operation, said: “Given the location and scale
of the task, it required a lot of detailed planning teamwork. It was a
truly collaborative project, with all parties contributing to the
successful end result.”
Ken Strong, managing director of Cool-
Therm, said: “We are delighted that a world-class company such as
Skandia has put its faith in Turbomiser. Following recent successful
installations at The Hilton, Stansted, and The Dorchester in London,
this project is further proof of the growing impact of Turbomiser
technology on the UK market.
He added: “I have no doubt that as
energy costs rise and pressure on companies to adopt sustainable
solutions increases, Turbomiser will become the chiller solution of
choice across a growing range of applications.”
Skandia has a
track record in pioneering approaches to energy and building
services.For many years it has been a key player in Southampton’s
groundbreaking district energy scheme. This provides high efficiency
heating and power to large public and commercial buildings across the
centre of the city, powered by a 5.7MW combined heat and power engine.
The scheme overall saves some 200,000 tonnes of carbon dioxide a year,
and provides low cost energy to a substantial proportion of the city’s
large buildings.
Click here to find out more about:
Cooltherm UK Ltd
N.B. The information contained in this entry is provided by the above supplier, and does not necessarily reflect the views and opinions of the publisher